The Body Structure is Stable
and Reliable
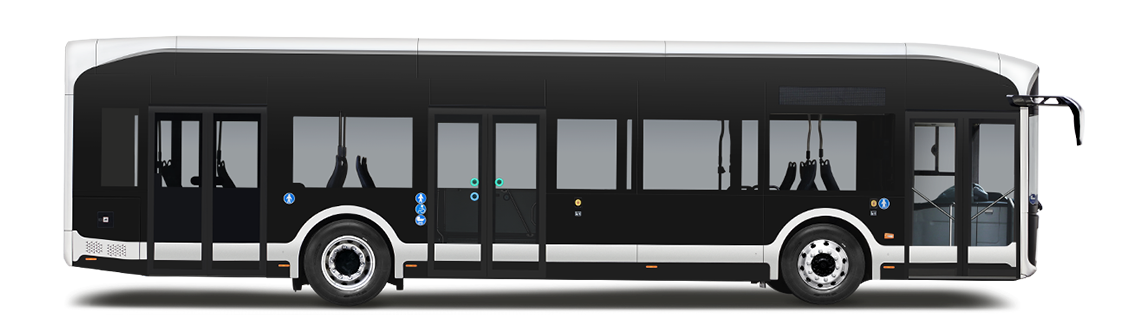
-
45°
Equipped with a super-strength closed-ring structure, the vehicle rollover angle can be up to 45° with minor rollover deformation.
-
-10%
With lightweight technology, 10%-20% weight reduction is realized and over 10% energy consumption reduced.
-
-10%
With the optimized aerodynamic streamline structure, the vehicles achieve wind resistance and energy consumption reduced by 10% and 5% respectively.
-
+50%
Box structure enables the shear resistance of roof and body frames up 50%.
-
-3mm
The Chinese character “日” shaped anti-collision beam structure makes the maximum deformation of side traction battery compartment anti-collision beam reduced by about 3 mm.
Durable and Reliable Material
-
High-Strength Materials Enhance the Body Frame Strength and Vehicle Rigidity
High-strength materials enhance the body frame strength and vehicle rigidity, thus improving the safety and reliability of vehicles.
-
The Front and Rear Walls Adopt Hot-Dip Galvanized Steel Panels
The front and rear walls adopt hot-dip galvanized steel panels, guaranteeing the flatness and strength of appearance, and solving the irreparable and ageing problems of the fiber reinforce plastic (FRP) front and rear wall panels.
-
The Bodyside and Top Cover Adopt Double-Sided Hot-Dip Galvanized Steel Panels with High Purity
The bodyside and top cover adopt double-sided hot-dip galvanized steel panels with high purity, good anti-sag and anti-rust performance, and high surface finish.
-
The Vehicle Doors Are Made of Aluminum Alloy
The vehicle doors are made of aluminum alloy, which is light, durable with strong anti-corrosion performance.
Application of Technical Processes
-
Argon mixed gas shielded welding ensures welding quality and avoids local failure expansion.
-
The pipe and harness layout and design are based on the separation concept to reduce potential hazards and facilitate maintenance.
-
Electrical protection system guarantees the safety of vehicle harness.
Subscribe Now
Get updates you care about.
Submit